The Full MRO Data Journey: Clean Data, Better Decisions
- IMA Ltd.
- Jul 16
- 3 min read
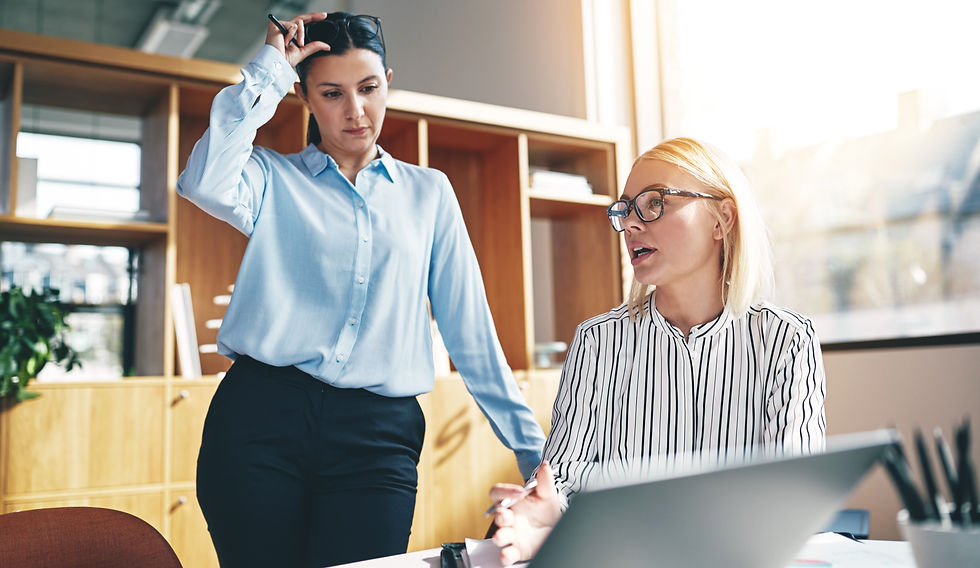
Maintenance, Repair, and Operations data is constantly evolving, and the way you manage it needs to evolve too. Every day new MRO data factors like vendors, materials and site needs are introduced. With no clear, continuous lifecycle strategy, even the cleanest dataset can quickly fall into chaos. That is why viewing MRO data as an ongoing journey, instead of a one time fix, is so critical. The journey begins with data collection, moves through cleansing and governance, and ultimately leads to the application of clean and improved data. In this blog, we will focus on the big picture of the MRO data lifecycle and explain how each step plays a role in keeping your operations efficient and effective.
Collection: Where It All Begins
A successful MRO data journey begins with data collection. Before data can be cleansed, governed and used, it first needs to be gathered from the many systems and locations where it is stored. At IMA, we offer both digital and onsite data collection services to help our clients gather information in the most efficient way possible.
We understand that some of the most valuable MRO data lives on the warehouse floors and in physical stockrooms. That is why IMA offers onsite data collection to capture this critical information firsthand. Our onsite team visits your facilities, inspects and verifies parts, materials, and inventory. Our hands on approach ensures that no data is overlooked specifically in environments where digital records may be outdated or incomplete. We want to help reconcile discrepancies between what’s on the shelf and what’s in the system.
IMA also provides a digital data collection service where we collect existing material master records from your business systems. The data is typically gathered from SAP exports, Maximo reports, Excel spreadsheets, and site managed files. These extract formats are structured to pull the relevant data fields such as material descriptions, part numbers, and inventory levels. An important part of the collection stage is aligning fields from different systems and sources, so they’re ready for the cleansing phase.
Whether onsite, digital, or a combination of both, data collection is the foundation of the entire MRO data lifecycle. Normally at this stage, organizations often uncover issues like inconsistent naming, typos, and duplicate records. Data collection through both physical and digital extracts is the essential first step toward cleaner, more efficient MRO data.
Cleansing: Standardizing and Deduplicating
Once the data has been collected, the next step is data cleansing. This step consists of standardizing material descriptions, removing duplicates, and aligning records. For example:
Before cleansing:
“3/8" brass ball valve”
“brs ball 3/8”
“Ball Valve 0.375in BR”.
After cleansing:
“Valve, 3/8 In, Brass”
Before data cleansing, there are endless variations in how items might appear in your material master, from inconsistent descriptions to duplicate entries and outdated records. Once the data is cleaned and standardized, new naming conventions and material standards are established, ensuring you always know exactly how your item records will appear moving forward.
Governance: Keeping Data Clean
Data governance is the process of maintaining the accuracy, consistency and reliability of your MRO data over time. It involves implementing policies, tools, and processes in place to protect data integrity as new materials are added. The governance phase typically includes: approval workflows for new part creation, regular audits and reporting to catch errors, and automated validation tools to flag issues in real time. uManage Pro, a solution provided by IMA, is designed as a tool to support the ongoing governance process.
Application: Using Clean Data to Drive Results
Clean MRO data is not just about organizing the mayhem; it is a powerful operational asset and a key driver of financial performance. With a new, clean, governed dataset, organizations can optimize inventory levels which reduces carrying costs. It can consolidate vendors and negotiate better pricing through improved visibility. Increase reliability by ensuring the right parts are available and enable maintenance strategies through accurate part data integration. In short, clean MRO data drives better insights that support more accurate, reliable procurement, maintenance, and supply chain teams.
Conclusion
At IMA, we believe that achieving clean, reliable MRO data isn’t a one time project; it’s an ongoing, continuous process. That is why our end-to-end services are designed to support the entire lifecycle of your data. Our approach begins with the initial collection of data using a variety of extract formats followed by a thorough cleansing process to standardize and organize scattered records. From there, we help organizations establish a governance framework that actively maintains data integrity, aligning with industry standards, and operational needs daily. The goal is to consistently improve, maintain and leverage data for real world business improvement. Ready to start your MRO data journey? Contact IMA today!
Comments